By Brett Campbell, MS-ENPH, CSP, Sr. Manager – Health & Safety Services, U.S. Compliance
Forklifts are indispensable tools in various industries, enabling efficient movement of heavy materials and contributing to the productivity of warehouses, manufacturing plants, and construction sites. However, despite their utility, forklifts can pose significant risks if not handled correctly. The leading causes of forklift accidents include rollovers, tip-overs, pedestrian collisions, falling loads, personnel falling from forks, and emissions poisoning. According to the Occupational Safety and Health Administration (OSHA), forklift accidents result in thousands of injuries each year, many of which are preventable through proper training and adherence to safety procedures.
This article highlights key forklift safety practices every operator and company should implement, from training and inspections to understanding forklift stability. Following these guidelines reduces accident risks, promotes a safer work environment, and enhances overall productivity.
1. Forklift Training
The first step in ensuring forklift safety is comprehensive training. OSHA mandates that all forklift operators undergo proper training and certification before operating equipment. Training should encompass both classroom instruction and practical, hands-on experience.
Operators must thoroughly understand how forklifts function, learn the different controls, and know how to respond to various situations they may encounter while operating the machinery. Training should also cover emergency procedures, load capacity limits, and the importance of regular equipment inspections.
Training should be ongoing, with refresher courses provided regularly, especially when new equipment or environments are introduced, after accidents or near-miss incidents, or when an operator is approaching the three-year certification mark. This continuous education ensures operators stay updated on safety practices and maintain high safety standards.
2. Daily Forklift Inspections
Forklift inspections are critical for identifying potential hazards before they lead to accidents or equipment failure. OSHA requires daily pre-shift inspections, which should be carried out by the operator or a designated safety personnel member.
The inspection checklist should include visual checks of tires, brakes, lights, the mast, and hydraulic systems. Operators should also verify the functionality of the horn, seat belt, and warning lights, and inspect the forks for any signs of wear or damage. Fluid levels, including oil, brake fluid, and hydraulic fluid, should be monitored to prevent malfunctions.
Any issues identified during the inspection must be addressed immediately before the forklift is used. This practice not only ensures operator safety but also extends the life of the equipment.
3. Maintain 360-Degree Visibility
Operating a forklift requires constant awareness of the surroundings and maintaining 360-degree visibility is vital for safe operation. Operators should always look in the direction of travel, ensuring that their path is clear of obstacles, people, and other machinery.
If carrying a load obstructs the operator’s view, it is safer to drive in reverse than move forward to maintain better visibility. Additionally, using mirrors, cameras, and other vision-enhancing devices can assist operators in detecting blind spots or other potential hazards. For optimal visibility, warehouse lighting should also be sufficient, and operators should wear high-visibility clothing when necessary.
4. Being Mindful of Safe Operating Distances
Maintaining a safe operating distance between forklifts, other machinery, and workers is essential. Forklifts, particularly when carrying loads, require ample space to maneuver and stop safely. Collisions are one of the most common causes of forklift accidents, often due to insufficient space between vehicles or between forklifts and pedestrians.
Forklift operators should follow the “three-vehicle-length” rule, maintaining a distance of at least three forklift lengths from other moving forklifts or objects. When stopping, operators should apply brakes smoothly and avoid sudden movements, which can cause tipping or cargo displacement.
5. Pedestrian Safety
Pedestrians are particularly vulnerable in workplaces where forklifts operate. Establishing clear pedestrian safety protocols is crucial in preventing accidents. Proper training is key, ensuring both operators and pedestrians understand safety procedures.
Pedestrian walkways should be clearly marked and separated from forklift routes. Crosswalks should be installed in areas where forklifts and pedestrians may intersect, and pedestrian zones should be clearly labeled with signs and floor markings. Operators must yield the right of way to pedestrians, use horns when approaching corners or crosswalks, and slow down in areas with high pedestrian traffic.
Pedestrians, in turn, should always maintain eye contact with the forklift operator and avoid walking or standing near operating forklifts whenever possible.
6. Establish Traffic Routes
Workplace traffic routes should be strategically designed to promote safe forklift operation. Clear and designated routes for forklifts, pedestrians, and other vehicles should be marked with signs, floor markings, and barriers where appropriate. Post signage for the speed limits and when to use horns, typically near blind corners and intersections.
Ideally, traffic routes will separate pedestrian paths from forklift routes. Where this is not possible, shared routes should be equipped with barriers, warning signs, and mirrors to prevent collisions. Pedestrians should use separate doors from forklifts and not share the same overhead doors.
A well-organized traffic management plan will help ensure that forklifts can operate without interference, reducing the likelihood of accidents and congestion in busy work environments.
7. Understand Forklift Stability
Understanding forklift stability is fundamental in preventing tipping accidents. Forklifts have a center of gravity that shifts depending on the load being carried and the angle of operation. Operators need to be aware of the “stability triangle,” which defines the points of balance between the forklift, the load, and the ground.
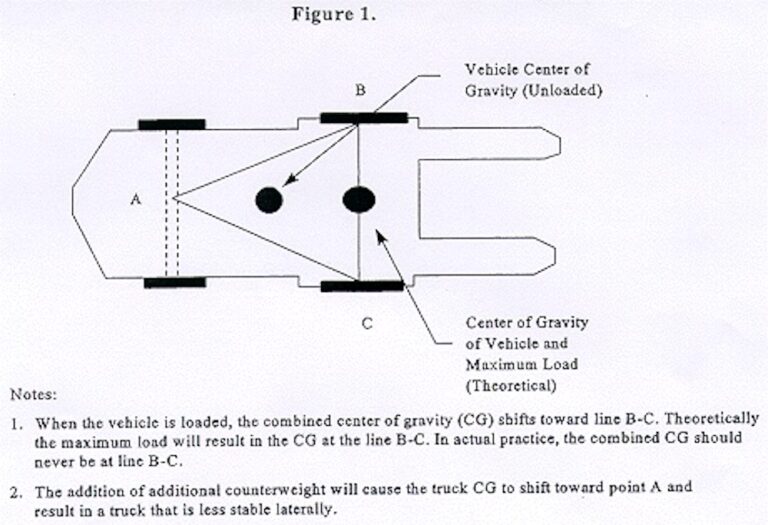
Carrying loads improperly, such as overloading or failing to distribute weight evenly, can compromise the forklift’s stability. Operators must also avoid driving on uneven surfaces or slopes, as this can also affect stability and increase the risk of tipping.
Training operators to calculate load limits and remain within the forklift’s rated capacity is essential for maintaining stability. Loads should always be carried low to the ground and tilted slightly back to keep the center of gravity stable.
8. Maintain Safe Speed
Speeding is a common contributor to forklift accidents. Operating a forklift at high speeds can reduce reaction time, increase the likelihood of tipping, and lead to collisions with pedestrians, structures, or other vehicles. To ensure safety, operators should adhere to speed limits set within the facility, particularly in areas with high pedestrian traffic or narrow aisles.
A safe speed varies depending on the environment, the weight of the load, and other factors, such as surface conditions. The best practice is to travel no faster than a walking speed around pedestrians or while carrying heavy loads. Operators should always reduce speed when making turns or when visibility is obstructed. Employers must enforce speed limits and ensure that operators understand the risks associated with high-speed operation.
9. Forklift Safety Devices
Modern forklifts are equipped with a variety of safety devices designed to enhance operator and pedestrian safety. These devices include seat belts, backup alarms, lights, and horns. Ensuring that these devices are in working order is critical for the safe operation of the equipment.
Some forklifts are also equipped with advanced safety technologies, such as proximity sensors, cameras, and automatic braking systems. These devices can help prevent accidents by alerting operators to nearby objects or pedestrians, and automatically stopping the forklift if a collision is imminent.
Employers should regularly inspect and maintain safety devices to ensure they function correctly, and operators should always use the equipment’s built-in safety features.
10. Enforce Safe Operation
Establishing and enforcing safe forklift operation policies is the responsibility of both employers and operators. Employers should create a culture of safety by providing ongoing training, implementing strict safety protocols, and regularly auditing forklift operations.
Supervisors must monitor operators to ensure compliance with safety rules, and any violations should be addressed promptly to prevent future incidents. Incentive programs that reward safe practices and penalties for unsafe behavior can also encourage adherence to safety standards.
For operators, understanding and following the company’s safety policies, communicating clearly with co-workers, and remaining vigilant while operating the forklift are all essential to preventing accidents.
Further, cellphone and headphone use on forklifts should not be permitted because it introduces significant distractions that can lead to accidents and injuries.
Conclusion
Forklift safety is a key component of workplace safety, requiring both proactive measures and ongoing vigilance. By providing thorough training, prioritizing pedestrian safety, and enforcing safe operation practices, companies can significantly reduce the risk of forklift accidents and create a safer, more efficient work environment.
Ensuring forklift safety is not only a regulatory requirement but also an investment in the well-being of employees and an organization’s overall success. For a complete list of forklift safety best practices, visit osha.gov to read OSHA Standard 1910.178. The standard outlines the general requirements for the operation of powered industrial lift trucks. Additionally, reach out to your U.S. Compliance representative for any questions or inquiries about forklift operator training.
Common Questions
Yes, OSHA requires that forklift inspections be documented. According to OSHA regulation 29 CFR 1910.178(q)(7), powered industrial trucks (including forklifts) must be inspected at least once daily before use. If a forklift is used continuously throughout multiple shifts, the inspection should occur at the beginning of each shift.
Here is what OSHA specifies regarding the documentation of these inspections:
- Inspection Documentation: While OSHA does not specifically state how long records of daily inspections must be kept, many companies document inspections to prove compliance in case of an audit or incident. This documentation provides a record that forklifts are being inspected regularly and any maintenance issues are addressed promptly.
- Purpose of Documentation: Keeping inspection records helps employers identify patterns in equipment performance, track recurring issues, and ensure that all safety protocols are followed. In the event of an accident or equipment malfunction, documented inspections can also serve as evidence that the company is following required safety procedures.
- What to Document: Inspections should include checking the brakes, tires, horns, lights, seat belts, mast, hydraulic systems, fluid levels, and any other relevant safety features. If any issues are found, they must be noted, and the forklift should not be used until repairs are made.
Although OSHA doesn’t mandate the format or duration of retaining the documentation, maintaining clear and consistent records is a best practice for ensuring compliance and supporting a culture of safety.
No, forklift operators are not required to complete the entire training process every three years, but OSHA does require that forklift operators undergo retraining in certain circumstances. According to OSHA regulation 29 CFR 1910.178(l)(4), retraining is necessary when:
- The operator has been involved in an accident or near-miss incident.
- The operator has been observed operating the forklift in an unsafe manner.
- The operator has received an evaluation that indicates unsafe operation.
- The operator is assigned to drive a different type of forklift.
- There are changes in the workplace that could affect safe operation, such as new layouts, hazards, or conditions.
Additionally, OSHA mandates that every three years, employers must evaluate the performance of forklift operators to ensure they continue to operate the equipment safely. If deficiencies are found during this evaluation, the operator must receive refresher training. However, if no issues are identified, full retraining may not be necessary.
For operators of motorized pallet jacks, OSHA requires the same fundamental training as for any other powered industrial truck, as outlined in 29 CFR 1910.178(l). The training must cover both formal instruction and hands-on practical training specific to the equipment being used.